Client: Wolf Creek Federal Services
Project: Demolition of 250MFH Units | Capehart III Housing Area | Andersen Air Force Base, Guam
Scope: Demolition of 250 Military Family Housing (MFH) Units at Capehart III Housing Area, Andersen Air Force Base, Guam. Works consisted of utility disconnections, reinforced masonry and concrete demolition, recycling of aluminium and steel debris, landscaping and turf reinstatement.
With a number of Military Family Housing (MFH) units at Andersen Air Force Base (AAFB) Guam, reaching their intended design life, NAVFAC Marianas through its Demolition Services Contractor, Wolf Creek Federal Services, commissioned demolition of 250 MFH units at Capehart III Housing Area, AAFB, Guam. The units earmarked for demolition will eventually be replaced with modern equivalents, but in the interim Wolf Creek Federal Services entrusted Smithbridge with the task of safely and efficiently demolishing the existing 250 units.
An extremely widespread project work site, covering an area in excess of one hundred and fifteen acres required multiple demolition teams. These teams were required to work closely alongside specialist HAZMAT technicians who removed asbestos, lead and freon in advance of demolition work activities. All work actives required detailed planning, preparation and communication. This was particularly the case as occupants and residents remained in nearby building facilities and schools adjacent to the work site throughout the duration of the demolition project.
Project Features
- 115 acre project site area
- 250 military housing units demolished
- 70,000 ton of debris hauled and disposed
- 6,200cuyd of topsoil
- 500,000sqft of grass seeding and maintenance
- Recycling of aluminum, structural and reinforcing steel building components
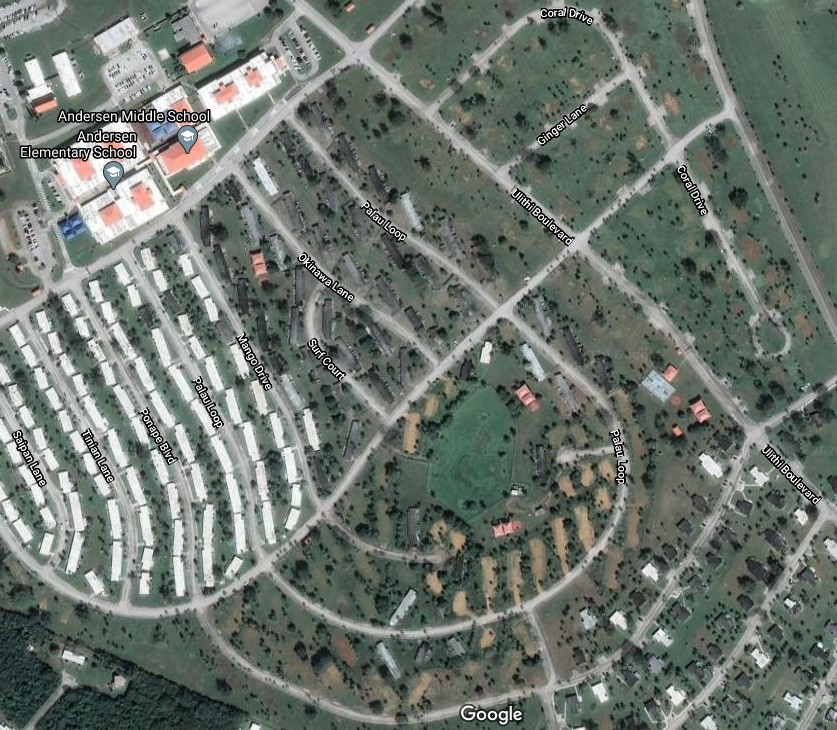
Innovative Construction Methodology – Large Excavators
Smithbridge provided two large 50t excavators – the extremely reliable Caterpillar 345 and Hyundai R500 machines – to accomplish the demolition work as safely and efficiently as possible with their respective crews. The use of large excavators allowed operators to distance their cabs from the interface between the bucket and structure, safely separating themselves from falling construction debris at all times during the demolition. The added horsepower of the large machines made relatively light work of the reinforced masonry and concrete structures, ensuring that the structures were demolished and loaded out for disposal as quickly as possible, minimizing both the construction schedule and potential disruption to neighboring building occupants and residents.
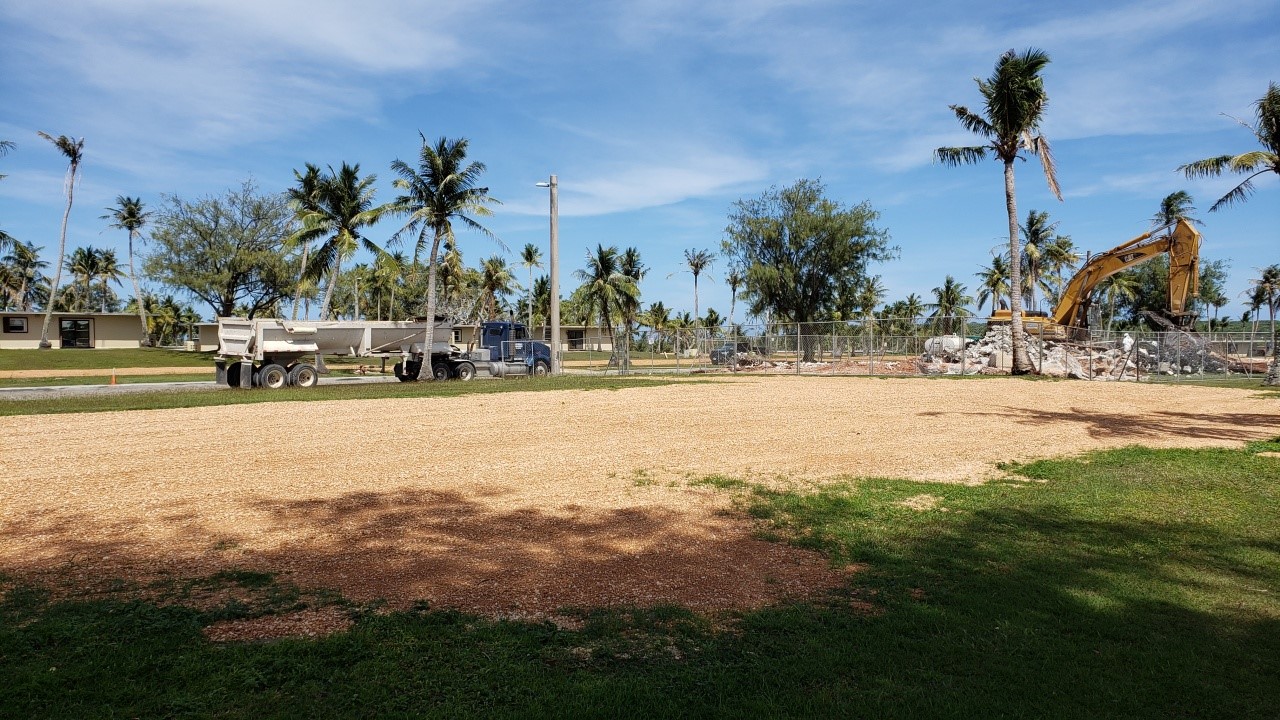
However, the nature of demolition work is that whilst most days the MFH units are demolished, there are some exceptions where there are days the excavator bucket teeth are demolished instead. Infrequent bucket repairs were a reminder of the large forces needed to bring these hardy MFH unit structures down, many of them designed to withstand potentially explosive blast forces from the Cold War era – see Figure 3 below for an example of Smithbridge’s repair team in action.
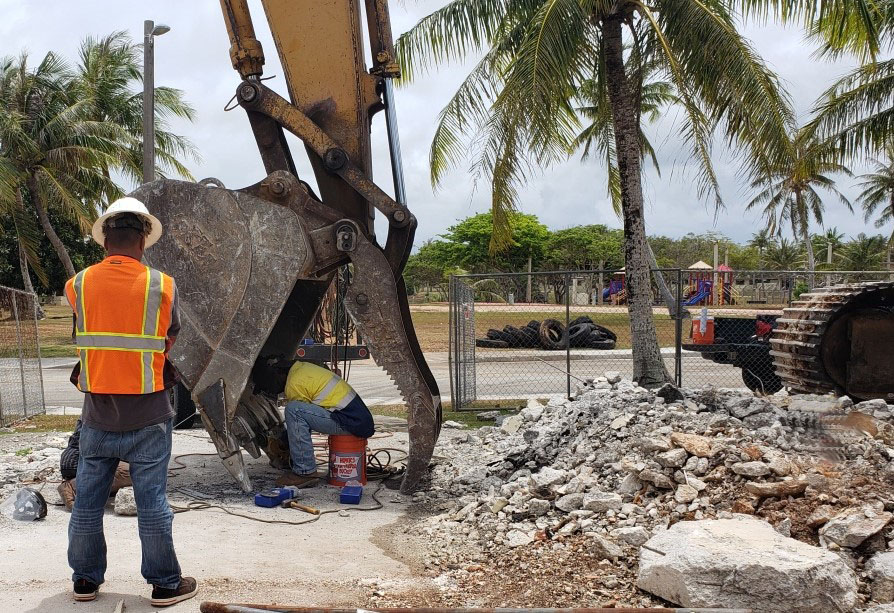
Innovative Construction Methodology – Haul Road Efficiency
Smithbridge identified a potential reduction in haul road distance, and successfully negotiated the use of the AAFB back gate with NAVFAC Marianas to provide a more direct disposal route from the demolition worksites to Smithbridge’s Guam EPA approved hardfill site in Yigo. The initiative relieved some truck congestion at the AAFB contractor’s gate and allowed a shorter turn around time for truck disposal movements also, which ultimately improved the efficiency of the demolition operation. Trucks maintained access into the demolition site via the AAFB contractor main gate for vehicle entry inspection purposes, ensuring that the strict AAFB vehicle entry and inspection requirements were adhered to at all times.
Innovative Construction Methodology – Topsoil Sourcing
Replacing the 250 MFH demolished units with four inches of new topsoil stretched local supply sources to their limits, requiring a total of approximately 6,200cuyd of topsoil. Whilst Smithbridge manufactured and delivered the majority of this quantity, the project made use of Maeda Pacific’s topsoil surplus from their concurrent Route 1 / Route 3 Intersection project performed for the Guam Department of Public Works. This utilization helped make best use of Guam’s precious local natural resources, whilst continuing Smithbridge’s commitment to the strict adherence of the demolition project specification requirements – see Figure 4 below for a typical Quality Assurance inspection of topsoil placed on one of the completed demolition sites.
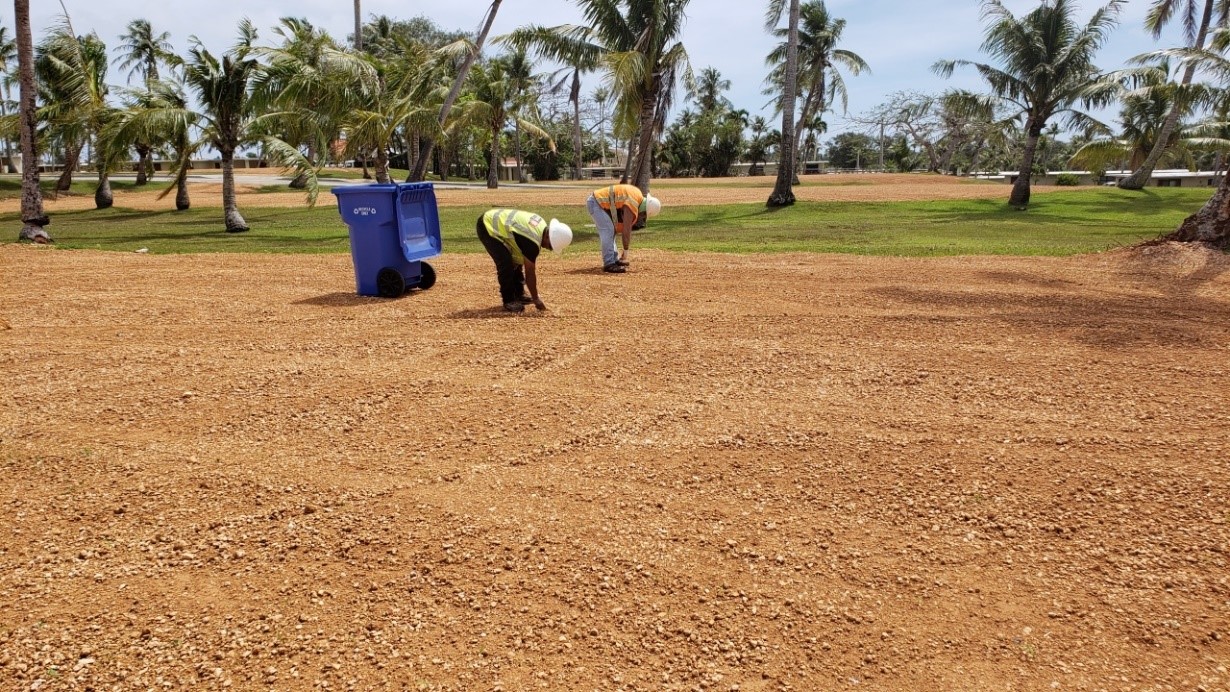
Innovative Personnel Management – Site Health and Safety Initiatives
The project management and site teams recognize the importance and priority personnel health and safety must take on all construction projects, and worked hard to develop and maintain a project specific safety management system that promoted safe work practices and ultimately led to 30,000 person hours completed on the project without a lost time injury or accident – an achievement the entire project team are extremely proud of.
Safe & Successful Completion
Smithbridge via Wolf Creek were fortunate enough to be entrusted with the safe and successful completion of the demolition project. A logistically difficult project at times given the vast project site area, with a good mix of traditional and innovative demolition techniques employed, was ultimately and most importantly, completed safely – primarily through the initial thoughtfulness of the construction methodology at project inception, and the excellent attitudes, culture and safe work practices adopted by the entire construction team during the physical work on site.
Winner of Excellence in Construction Award 2020
As part of the Guam Contractor’s Association annual Excellence in Construction Awards in 2020, this project won in the category of Federal Government / Military (Less than $10 Million). The Excellence in Construction Awards promote quality craftsmanship in the industry and celebrate and reward construction projects across Guam. The awards have been running in Guam since 1997 and are a prestigious honour and coveted award to receive in such a competitive industry.